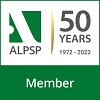
Efficient Exergy Analysis of Chemical Processes through Process Engineering Software
DOI:
https://doi.org/10.30564/jcsr.v6i3.6720Abstract
In this work, authors present a simple methodology for computing physical, chemical and total exergies, and the exergy destruction and the exergetic efficiency of simple and complex processes by using the object linking and embedded (OLE) automation by connecting Aspen HYSYS to MS Excel VBA. For this purpose, a simple flowsheet was added to the main one with the same number of streams as that of the components. By introducing all these streams in a mixer and then consecutively conducted to a heater to condition the outlet stream, a separator and a mixer, the VBA application was able to compute the chemical exergy of the different streams of the main flowsheet. To demonstrate the procedure here described seven cases were considered: single streams, a CO2 mixer, a cooler, a distillation column, a reactor, a multiple recirculation process, and different configurations of separating components by distillation, which can be extended to very complex processes. The former was selected to validate the methodology here proposed whereas the rest of cases were used to demonstrate the potential of the tool here developed, which in turn could be used for discriminating among different process alternatives.
Keywords:
Automation; Simulators; MS Excel-VBA; Exergy analysisReferences
[1] Mendonça Teixeira, A., de Oliveira Arinelli, L., de Medeiros, J. L., et al., 2018. Monoethylene Glycol as Hydrate Inhibitor in Offshore Natural Gas Processing. In SpringerBriefs in Petroleum Geoscience and Engineering. Springer International Publishing: NY. DOI: https://doi.org/10.1007/978-3-319-66074-5
[2] Rosen, M.A., 2021. Exergy Analysis as a Tool for Addressing Climate Change. European Journal of Sustainable Development Research. 5(2), em0148. DOI: https://doi.org/10.21601/ejosdr/9346
[3] Kilkis, B., 2019. Decarbonization: exergy to the rescue. In CLIMA 2019 conference, 26–29 May, Bucharest. p. 26-29.
[4] Blanco, J., Linares, M., López Granados, M., et al., 2022. Integrated Environmental and Exergoeconomic Analysis of Biomass‐Derived Maleic Anhydride. Advanced Sustainable Systems. 6(9). DOI: https://doi.org/10.1002/adsu.202200121
[5] Luis, P., Van der Bruggen, B., 2014. Exergy analysis of energy‐intensive production processes: advancing towards a sustainable chemical industry. Journal of Chemical Technology and Biotechnology. 89(9), 1288–1303. DOI: https://doi.org/10.1002/jctb.4422
[6] Nimkar, S.C., Mewada, R.K., 2014. An overview of exergy analysis for chemical process industries. International Journal of Exergy. 15(4), 468. DOI: https://doi.org/10.1504/ijex.2014.066614
[7] Sciubba, E., 2019. Exergy-based ecological indicators: From Thermo-Economics to cumulative exergy consumption to Thermo-Ecological Cost and Extended Exergy Accounting. Energy. 168, 462–476. DOI: https://doi.org/10.1016/j.energy.2018.11.101
[8] Liu, X., Liu, F., Huo, Z., et al., 2022. Exergy and Exergoeconomic Analyses of a Byproduct Gas-Based Combined Cycle Power Plant with Air Blade Cooling. ACS Omega. 7(6), 4908–4920. DOI: https://doi.org/10.1021/acsomega.1c05502
[9] Aliyu, M., AlQudaihi, A.B., Said, S.A.M., et al., 2020. Energy, exergy and parametric analysis of a combined cycle power plant. Thermal Science and Engineering Progress. 15, 100450. DOI: https://doi.org/10.1016/j.tsep.2019.100450
[10] Seyyedi, S.M., Ajam, H., Farahat, S., 2010. A new criterion for the allocation of residues cost in exergoeconomic analysis of energy systems. Energy. 35(8), 3474–3482. DOI: https://doi.org/10.1016/j.energy.2010.04.047
[11] Luo, X., Hu, J., Zhao, J., et al., 2014. Improved exergoeconomic analysis of a retrofitted natural gas-based cogeneration system. Energy. 72, 459–475. DOI: https://doi.org/10.1016/j.energy.2014.05.068
[12] Gao, J., Zhang, Q., Wang, X., et al., 2018. Exergy and exergoeconomic analyses with modeling for CO2 allocation of coal-fired CHP plants. Energy. 152, 562–575. DOI: https://doi.org/10.1016/j.energy.2018.03.171
[13] Özen, D.N., Koçak, B., 2022. Advanced exergy and exergo-economic analyses of a novel combined power system using the cold energy of liquefied natural gas. Energy. 248, 123531. DOI: https://doi.org/10.1016/j.energy.2022.123531
[14] El Haj Assad, M., Aryanfar, Y., Javaherian, A., et al., 2021. Energy, exergy, economic and exergoenvironmental analyses of transcritical CO2 cycle powered by single flash geothermal power plant. International Journal of Low-Carbon Technologies. 16(4), 1504–1518. DOI: https://doi.org/10.1093/ijlct/ctab076
[15] Lara, Y., Petrakopoulou, F., Morosuk, T., et al., 2017. An exergy-based study on the relationship between costs and environmental impacts in power plants. Energy. 138, 920–928. DOI: https://doi.org/10.1016/j.energy.2017.07.087
[16] Kumar, R., 2017. A critical review on energy, exergy, exergoeconomic and economic (4-E) analysis of thermal power plants. Engineering Science and Technology, an International Journal. 20(1), 283–292. DOI: https://doi.org/10.1016/j.jestch.2016.08.018
[17] Petrakopoulou, F., Tsatsaronis, G., Morosuk, T., et al., 2012. Conventional and advanced exergetic analyses applied to a combined cycle power plant. Energy. 41(1), 146–152. DOI: https://doi.org/10.1016/j.energy.2011.05.028
[18] Alibaba, M., Pourdarbani, R., Manesh, M.H.K., et al., 2020. Thermodynamic, exergo-economic and exergo-environmental analysis of hybrid geothermal-solar power plant based on ORC cycle using emergy concept. Heliyon. 6(4), e03758. DOI: https://doi.org/10.1016/j.heliyon.2020.e03758
[19] Fani, M., Norouzi, N., Ramezani, M., 2020. Energy, Exergy, and Exergoeconomic Analysis of Solar Thermal Power Plant Hybrid with Designed PCM Storage. International Journal of Air-Conditioning and Refrigeration. 28(4), 2050030. DOI: https://doi.org/10.1142/s2010132520500303
[20] Cavalcanti, E.J.C., Carvalho, M., B. Azevedo, J.L., 2019. Exergoenvironmental results of a eucalyptus biomass-fired power plant. Energy. 189, 116188. DOI: https://doi.org/10.1016/j.energy.2019.116188
[21] Koroglu, T., Sogut, O.S., 2018. Conventional and advanced exergy analyses of a marine steam power plant. Energy. 163, 392–403. DOI: https://doi.org/10.1016/j.energy.2018.08.119
[22] Ferrara, G., Lanzini, A., Leone, P., et al., 2017. Exergetic and exergoeconomic analysis of post-combustion CO2 capture using MEA-solvent chemical absorption. Energy. 130, 113–128. DOI: https://doi.org/10.1016/j.energy.2017.04.096
[23] Soltani, S., Mahmoudi, S.M.S., Yari, M., et al., 2013. A comparative exergoeconomic analysis of two biomass and co-firing combined power plants. Energy Conversion and Management. 76, 83–91. DOI: https://doi.org/10.1016/j.enconman.2013.07.030
[24] Petrakopoulou, F., Boyano, A., Cabrera, M., et al., 2011. Exergoeconomic and exergoenvironmental analyses of a combined cycle power plant with chemical looping technology. International Journal of Greenhouse Gas Control. 5(3), 475–482. DOI: https://doi.org/10.1016/j.ijggc.2010.06.008
[25] Cavalcanti, E.J.C., Carvalho, M., da Silva, D.R.S., 2020. Energy, exergy and exergoenvironmental analyses of a sugarcane bagasse power cogeneration system. Energy Conversion and Management. 222, 113232. DOI: https://doi.org/10.1016/j.enconman.2020.113232
[26] Hofmann, M., Tsatsaronis, G., 2018. Comparative exergoeconomic assessment of coal-fired power plants – Binary Rankine cycle versus conventional steam cycle. Energy. 142, 168–179. DOI: https://doi.org/10.1016/j.energy.2017.09.117
[27] Wu, J., Wang, N., 2020. Exploring avoidable carbon emissions by reducing exergy destruction based on advanced exergy analysis: A case study. Energy. 206, 118246. DOI: https://doi.org/10.1016/j.energy.2020.118246
[28] Lazzaretto, A., Tsatsaronis, G., 2006. SPECO: A systematic and general methodology for calculating efficiencies and costs in thermal systems. Energy. 31(8–9), 1257–1289. DOI: https://doi.org/10.1016/j.energy.2005.03.011
[29] Dias, F.P.F., Fernandes, I.T., Bueno, A.V., et al., 2021. Exergy analysis of glycerol steam reforming in a heat recovery reactor. International Journal of Hydrogen Energy. 46(13), 8995–9007. DOI: https://doi.org/10.1016/j.ijhydene.2020.12.215
[30] Yaqoob, H., Teoh, Y.H., Sher, F., et al., 2022. Energy, exergy, sustainability and economic analysis of waste tire pyrolysis oil blends with different nanoparticle additives in spark ignition engine. Energy. 251, 123697. DOI: https://doi.org/10.1016/j.energy.2022.123697
[31] Zhang, Y., Xu, P., Liang, S., et al., 2019. Exergy analysis of hydrogen production from steam gasification of biomass: A review. International Journal of Hydrogen Energy. 44(28), 14290–14302. DOI: https://doi.org/10.1016/j.ijhydene.2019.02.064
[32] Sorin, M., Lambert, J., Paris, J., 1998. Exergy Flows Analysis in Chemical Reactors. Chemical Engineering Research and Design. 76(3), 389–395. DOI: https://doi.org/10.1205/026387698524811
[33] Blumberg, T., Morosuk, T., Tsatsaronis, G., 2017. Exergy-based evaluation of methanol production from natural gas with CO2 utilization. Energy. 141, 2528–2539. DOI: https://doi.org/10.1016/j.energy.2017.06.140
[34] Vilarinho, A.N., Campos, J.B.L.M., Pinho, C., 2016. Energy and exergy analysis of an aromatics plant. Case Studies in Thermal Engineering. 8, 115–127. DOI: https://doi.org/10.1016/j.csite.2016.06.003
[35] Tesch, S., Morosuk, T., Tsatsaronis, G., 2016. Advanced exergy analysis applied to the process of regasification of LNG (liquefied natural gas) integrated into an air separation process. Energy. 117, 550–561. DOI: https://doi.org/10.1016/j.energy.2016.04.031
[36] Ibrahim, A. Y., Ashour, F. H., Gadalla, M. A., 2021. Exergy study of amine regeneration unit using diethanolamine in a refinery plant: A real start-up plant. Heliyon. 7(2), e06241. DOI: https://doi.org/10.1016/j.heliyon.2021.e06241
[37] Ghannadzadeh, A., Thery-Hetreux, R., Baudouin, O., et al., 2012. General methodology for exergy balance in ProSimPlus® process simulator. Energy. 44(1), 38–59. DOI: https://doi.org/10.1016/j.energy.2012.02.017
[38] Gourmelon, S., Thery-Hetreux, R., Floquet, P., et al., 2015. Exergy analysis in ProSimPlus® simulation software: A focus on exergy efficiency evaluation. Computers & Chemical Engineering. 79, 91–112. DOI: https://doi.org/10.1016/j.compchemeng.2015.02.014
[39] Mestre-Escudero, R., Puerta-Arana, A., González-Delgado, Á.D., 2020. Process Simulation and Exergy Analysis of a Mercaptan Oxidation Unit in a Latin American Refinery. ACS Omega. 5(34), 21428–21436. DOI: https://doi.org/10.1021/acsomega.0c01791
[40] Gollangi, R.K.N., 2022. Energy, exergy analysis of conceptually designed monochloromethane production process from hydrochlorination of methanol. Energy. 239, 121858. DOI: https://doi.org/10.1016/j.energy.2021.121858
[41] Gollangi, R., Nagamalleswara Rao, K., 2022. Energetic, exergetic analysis and machine learning of methane chlorination process for methyl chloride production. Energy & Environment. 34(7), 2432–2453. DOI: https://doi.org/10.1177/0958305x221109604
[42] Abdollahi-Demneh, F., Moosavian, M.A., Omidkhah, M.R., et al., 2011. Calculating exergy in flowsheeting simulators: A HYSYS implementation. Energy. 36(8), 5320–5327. DOI: https://doi.org/10.1016/j.energy.2011.06.040
[43] Santos Bartolome, P., Van Gerven, T., 2022. A comparative study on Aspen Hysys interconnection methodologies. Computers & Chemical Engineering. 162, 107785. DOI: https://doi.org/10.1016/j.compchemeng.2022.107785
[44] Valverde, J.L., Ferro, V.R., Giroir‐Fendler, A., 2022. Automation in the simulation of processes with Aspen HYSYS: An academic approach. Computer Applications in Engineering Education. 31(2), 376–388. DOI: https://doi.org/10.1002/cae.22589
[45] Valverde JL, G.-F. A., Ramírez A, Ferro VR, 2023. Use of automation to link aspen hysys with third-party software for simulating complex chemical engineering problems. Austin Chemical Engineering. 10 (3), 1105.
[46] Valverde JL, F.V., Barbero-Sánchez J, Giroir-Fendler A., 2023. Automation of process simulations with aspen plus. Austin Chemical Engineering. 10(2), 1099.
[47] Barbero-Sánchez, J., Megía-Ortega, A., R. Ferro, V., et al., 2024. Exploring Alternatives to Create Digital Twins from and for Process Simulation. Journal of Computer Science Research. 6(1), 16–30. DOI: https://doi.org/10.30564/jcsr.v6i1.6168
[48] Bejan, A., Tsatsaronis, G., Moran, M.J., 1995. Thermal design and optimization. John Wiley and Sons: NJ.
[49] Dincer, I., Rosen, M.A., 2021. Chemical exergy. Exergy. 37–60. DOI: https://doi.org/10.1016/b978-0-12-824372-5.00003-8
[50] Xiang, J. Y., Calì, M., Santarelli, M., 2004. Calculation for physical and chemical exergy of flows in systems elaborating mixed-phase flows and a case study in an IRSOFC plant. International Journal of Energy Research. 28(2), 101–115. DOI: https://doi.org/10.1002/er.953
[51] Szargut, J., Morris, D.R., Steward, F.R., 1987. Exergy analysis of thermal, chemical, and metallurgical processes. Available from: https://www.osti.gov/biblio/6157620 (cited 10 May 2024).
[52] Seider, W.D., Lewin, D.R., Seader, J.D., et al., 2017. Product and process design principles: synthesis, analysis and evaluation. John Wiley and Sons: NJ
[53] Valverde, J.L., Ferro, V.R., Giroir‐Fendler, A., 2022. Automation in the simulation of processes with Aspen HYSYS: An academic approach. Computer Applications in Engineering Education. 31(2), 376–388. DOI: https://doi.org/10.1002/cae.22589
[54] Luyben, W.L., Tyréus, B.D., Luyben, M.L., 1999. Plantwide process control. McGraw-Hill Professional Publishing: McGraw Hill.
[55] C Matsui, E., Van Le, V., 2023. Exergy, energy, economic, and environmental assessment of gas condensate stabilization units for the selection of optimum configuration. Advances in Engineering and Intelligence Systems. 2(1), 111–128.
Downloads
How to Cite
Issue
Article Type
License
Copyright © 2024 Author(s)

This is an open access article under the Creative Commons Attribution-NonCommercial 4.0 International (CC BY-NC 4.0) License.